EMI Shielding Products
- Custom Gasket Fabrication
- Connector Gaskets
- Bonded O Ring
- Custom Gaskets
- Conduct-O-Knit Knitted Wire Mesh
- Conduct-O-Seal Combo Gasket
- Conduct-O-Elastomer
- Conduct-O-Seal Oriented Wire in Silicone Gasket Material
- Conduct-O-Mesh Tape
- Conduct-O-Foam
- Conduct-O-Bond
- Optical Filters For Electronic Displays
- Shielded Vent Panels
- ESC Board Level Shielding
- 300 Series
How to Prevent Corrosion When Creating EMI Shielding Devices
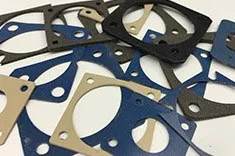
Electromagnetic interference (EMI) refers to unwanted interference or noise in a circuit or electrical path. This interference is caused by an outside source, such as electrical devices or lightning. EMI has many adverse effects and can lead to electronics operating poorly or malfunctioning. In this high-tech world, shielding EMI is essential. Designing efficient EMI shielding devices is vital to ensure they are not affected by outside sources.
When creating EMI shielding devices, there are many features to consider. The prevention of corrosion is one key factor to consider. Let's review some steps to prevent corrosion when creating EMI shielding devices.
- The most crucial step is to consider the environment. Devices exposed to the elements, such as humidity and water, will be more prone to corrosion.
- Small parts with less space will benefit from electrically conductive rubber gaskets. These gaskets can be cut to specific dimensions.
- Consider using a combined gasket for larger parts, such as an EMI gasket with a water seal made of silicone, EPDM rubber, or neoprene.
- It's important to consider exposure to the sea when choosing gasket material.
- When the device's metal is sensitive to corrosion, consider applying a finishing material like nickel or chrome. Applying a finish helps the surface to maintain its required conductivity. While materials like zinc-plated steel or aluminum can prevent corrosion, they provide less conductivity.
- When choosing the material for your gasket, it's important to consider temperatures. Neoprene can withstand freezing and boiling temperatures. Silicone rubber can handle the highest temperatures, up to 220 degrees Celsius.