EMI Shielding Products
- Custom Gasket Fabrication
- Connector Gaskets
- Bonded O Ring
- Custom Gaskets
- Conduct-O-Knit Knitted Wire Mesh
- Conduct-O-Seal Combo Gasket
- Conduct-O-Elastomer
- Conduct-O-Seal Oriented Wire in Silicone Gasket Material
- Conduct-O-Mesh Tape
- Conduct-O-Foam
- Conduct-O-Bond
- Optical Filters For Electronic Displays
- Shielded Vent Panels
- 300 Series
Spliced and Molded EMI Shielding Gaskets
EMI shielding gaskets are sold in several different materials with a limitless amount of sizes and shapes. Typically, base materials are made from fluorosilicone or silicon that has fillers like silver, silver-plated aluminum, and nickel-plated graphite. These conductive elastomers are one of the most versatile products for EMI shielding gaskets.
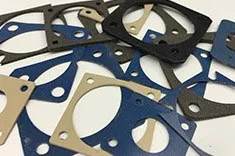
Manufacturers use two main processes to create gaskets:
Splicing: this process fuses together extruded ends to create custom O-rings. When finished, parts have an immensely strong bond.
Advantages of splicing include:
- They require little or no tooling, which translates to low upfront capital investments
- They are used with hollow cross-section profiles that allow for creating parts that accommodate low compression force enclosures
- Bulk material can be extruded in long lengths
- Quicker turnaround times
Molding: this process compresses uncured conductive elastomers into a custom designed mold. Materials take and maintain shapes after being cured.
Advantages of molding include:
- Complex parts are easily joined in a variety of cross sections across one part
- Easily hold tolerances within a thousandth of an inch
- Retains the shape of the mold that created them
- Commonly made in tiny O-rings and parts
EMI Shielding
Both manufacturing methods produce almost endless numbers of shapes and profiles. Just as splicing and molding have their benefits, they also have disadvantages. Weighing the pros and cons is the best way to pick a manufacturing method. If you need more information for designing EMI shielding gaskets, you should contact our talented team.
Related Reading:
- Different Emi Shielding and EMI Gasket TypesWhen buying gaskets, it is essential to understand the differences between different geometry and materials. Although both offer different characteristics, all gaskets can be broken down into four essential types.
- EMI shielding Effectiveness Testing
- EMI Shielding and the Military
- Design Tips for EMI Shielding Corrosion Resistance