EMI Shielding Products
- Custom Gasket Fabrication
- Connector Gaskets
- Bonded O Ring
- Custom Gaskets
- Conduct-O-Knit Knitted Wire Mesh
- Conduct-O-Seal Combo Gasket
- Conduct-O-Elastomer
- Conduct-O-Seal Oriented Wire in Silicone Gasket Material
- Conduct-O-Mesh Tape
- Conduct-O-Foam
- Conduct-O-Bond
- Optical Filters For Electronic Displays
- Shielded Vent Panels
- 300 Series
Manufacturing Options for EMI Shielding
The purpose of EMI shields is to protect and extend the performance of electrical devices by creating conductive paths between two surfaces. EMI shielding gaskets work to ensure that the necessary levels of electrical conductivity are maintained. Without a shielding gasket, devices will transmit EMI disturbances into the surrounding world that negatively affect electrical circuits in other devices.
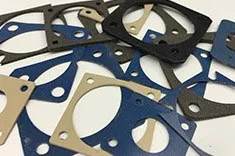
There are many causes of EMI in the world, both natural and human-made, so it is essential for engineers to factor in electromagnetic stimulation. There are four main methods of manufacturing EMI shielding gaskets.
Engineers must choose more than just the materials to be used. People must also consider the relationships that are formed between form factors and methods of gasket fabrication.
The four ways to form EMI shielding gaskets are:
- Die cutting: this method of forming produces many parts in a relatively short amount of time. The process is repeatable, effective, and quick. Die cutting is excellent for making nested parts that have punched holes and slots.
- Extrusion: extrude EMI gaskets are perfect for groove and flange applications. Different shapes are available to offer unique characteristics.
- Molded: EMI shields made in this way to create effective means of reducing cost through eliminating center drop waste that is associated with die cutting. This method of forming is widely used because it offers solutions for many problems die cutting and extrusion cannot fix.
- Form-in-place: this method of production creates excellent solutions for complicated and sophisticated designs. The process easily accommodates densely populated electronic cases where complex cross-sections and isolation patterns are required.
EMI Shielding
- Design Tips for EMI Shielding Corrosion ResistanceYou must select the correct EMI gasket, which can help to slow down corrosion by offering lower galvanic currents.
- EMI and Consumer Products
- Spliced and Molded EMI Shielding Gaskets
- Popular Materials for EMI Shields and Gaskets